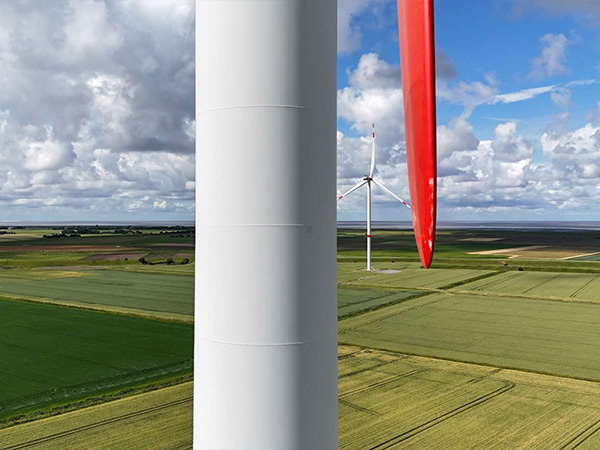
Visual inspections
Ground-based: quick but less detailed.
Rope access: detailed but time-consuming.
Drones: a highly effective and economical method for close-up inspections, allowing for comprehensive
Analysis without extended downtime.
Blade inspections are vital for the safe, efficient, and cost-effective operation of wind turbines. Regular checks help detect damage early, reduce repair costs, and extend the lifespan of blades, directly impacting energy production and profitability. Advances in technology, such as drones and robotics, have significantly improved the efficiency and precision of inspections, making them a critical component of any wind farm’s maintenance strategy. Common blade issues, such as leading-edge erosion, cracks, surface wear, and lightning damage—responsible for 25% of blade damages—can all be effectively managed through regular, thorough inspections. Prioritizing inspections allows turbine operators to prevent long-term damage, reduce operational costs, and ensure the reliable operation of their turbines.
Key repair types:
- Coating repairs
- Laminate repairs
- Balsa/core replacement
- Vortex generator & serration repairs
- Leading edge erosion repair
- Structural crack repairs
- Bondline inspection and repair
- Tip repairs
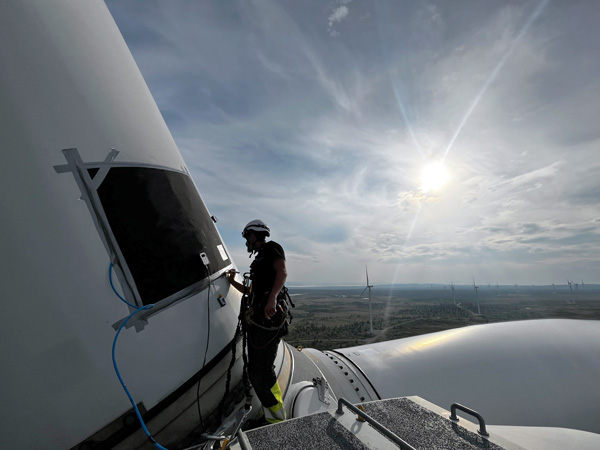
STRUCTURAL REPAIRS AND LAMINATION
Structural repairs focus on maintaining the integrity of blades made from composite materials like fiberglass and carbon fiber. Damage caused by fatigue stress, lightning strikes, or erosion can weaken the blade’s performance and must be addressed quickly.
CAUSES OF DAMAGE AND DELAMINATION
- Fatigue stress: continuous wind exposure weakens the structure.
- Moisture ingress: water weakens the bonds between layers, often leading to delamination.
- Thermal stress: temperature changes can affect the adhesive bonds.
- Mechanical impacts: objects striking the blade can cause cracks and dents.
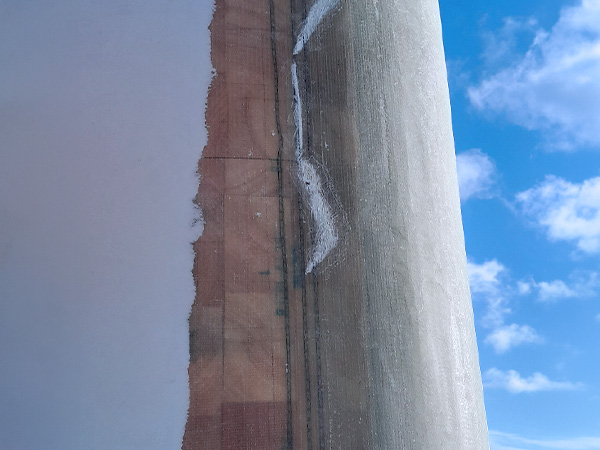
When are temporary repairs needed?
- Weather constraints: unsafe conditions such as high winds or freezing temperatures.
- Remote locations: difficult-to-access turbines where logistics hinder full repairs.
- Limited access to materials: lack of specialized materials or technicians.
- Preventing further damage: addressing small issues before they escalate.
COMMON TYPES OF TEMPORARY BLADE REPAIRS
- Surface crack sealing: using quick-curing sealants to prevent moisture intrusion and crack propagation.
- Patch repairs: applying composite material patches to minor damages to protect against worsening.
- Temporary leading edge protection (lep): using durable films to shield the leading edge from erosion.
- Temporary structural reinforcements: installing braces or straps to stabilize compromised areas.
- Bondline reinforcement: applying temporary adhesives or fasteners to maintain section integrity.
- Temporary serration and vortex generator replacement: replacing or reattaching damaged components to preserve aerodynamic performance.
MATERIALS USED IN TEMPORARY REPAIRS
- Epoxy resins: for sealing cracks and reinforcing damaged areas.
- Lep tape: for leading edge protection.
- Fast-curing adhesives: for applying patches and components.
- Composite materials: such as fiberglass or polyester for patch repairs.
CHALLENGES AND RISKS OF TEMPORARY REPAIRS
- Limited lifespan: require regular monitoring to prevent failure.
- Reduced structural integrity: often provide minimal reinforcement.
- Aerodynamic efficiency: may alter blade profile and reduce turbine efficiency.
- Weather-related wear: vulnerable to degradation from harsh conditions.
INSPECTION AND MONITORING AFTER TEMPORARY REPAIRS
Continuous monitoring is critical, involving:
- Drone inspections: for hard-to-reach areas.
- Manual inspections: regular visual checks by technicians.
- Sensor data: embedded sensors provide real-time stress and strain information.
TRANSITION TO PERMANENT REPAIRS
Temporary repairs must be followed by comprehensive solutions, such as:
- Full re-lamination: to restore structural integrity.
- Leading edge re-coating: for long-term erosion protection.
- Component replacement: installing permanent parts for efficiency.
- Structural bondline repair: high-strength re-bonding of sections.
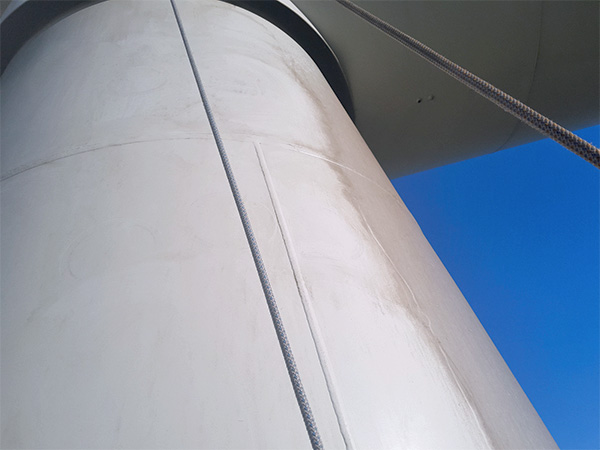
IMPORTANCE OF CLEANING OIL/GREASE LEAKS
Wind turbines require lubricants and hydraulic fluids for efficient operation. Prompt cleaning of oil and grease leaks is essential for:
- Environmental protection: prevents pollution in sensitive areas, such as rural and offshore locations.
- Safety concerns: reduces slip hazards for maintenance workers.
- Component protection: prevents further damage to seals and bearings, avoiding costly repairs.
- Turbine performance: ensures optimal lubrication, preventing overheating and mechanical failures.
- Visual impact: maintains the turbine’s appearance and complies with clean energy regulations.
CHALLENGES IN CLEANING
Cleaning presents unique challenges:
- Height and accessibility: requires specialized equipment for tall structures.
- Weather conditions: operations can be delayed by adverse weather.
- Environmental sensitivity: care is needed to avoid contaminating ecosystems.
PREVENTIVE MEASURES
Operators can reduce leaks by:
- Regular inspections: early detection of small leaks.
- Seal maintenance: routine checks and replacements of seals.
- Lubricant monitoring: keeping track of lubricant levels to prevent wear.
- Advanced materials: using long-lasting seals and lubricants.